Transforming Small Batch Production
We recently had the privilege of speaking to one of our valued customers about their journey to overcome significant production challenges. Their story is one of resilience, innovation, and collaboration as they sought a solution to meet the demands of their pharmaceutical production processes.
This customer produces life-saving products that treats serious diseases, significantly impacting patients’ lives. However, their production is highly specialized, with batches sometimes limited to as few as 100 units. Despite the small scale, they were relying on packaging systems designed for large-scale production – a practice that was no longer sustainable. Recognizing the inefficiencies, they decided to rethink their processes and explore innovative solutions for producing very small batches.
Rethinking Production: A New Way of Working
Reducing Changeover Time
When the Customer and their team began exploring alternatives, they quickly realized that adopting a new approach wasn’t straightforward. They engaged with several technology providers to understand how modern solutions could streamline their processes.
One of the key challenges identified was the excessive time lost during changeovers. Traditional methods required up to 8 hours – or more – to set-up, clean, and execute equipment line clearance, while the actual production of small batches only took a few minutes. Reducing this changeover time became a top priority for the customer.
Managing format changes was another significant challenge, with extensive adjustments required for each batch. This inefficiency highlighted the need for a more flexible solution. After careful evaluations, it became clear that robotic technology offered the adaptability they needed.
The focus then shifted to finding the right partner—a manufacturer capable of providing a robotic bottle-filling line that could meet their demands. Ultimately, they needed to identify a partner who could deliver the precision and efficiency required to transform their production process.

A prototype of a robotic solution for bottles
Optimizing Space
Space constraints posed another significant obstacle. A traditional packaging line required numerous machines – bottle blowers, fillers, torque machines, labellers, cartoners, case packers, and palletizers – spread across at least 40 meters. Connecting all this equipment consumed valuable floor space and complicated the process.
By adopting a modular and integrated solution, they would be able to consolidate these steps into a much smaller footprint. Flexible, interconnected modules would make production far more space effective.
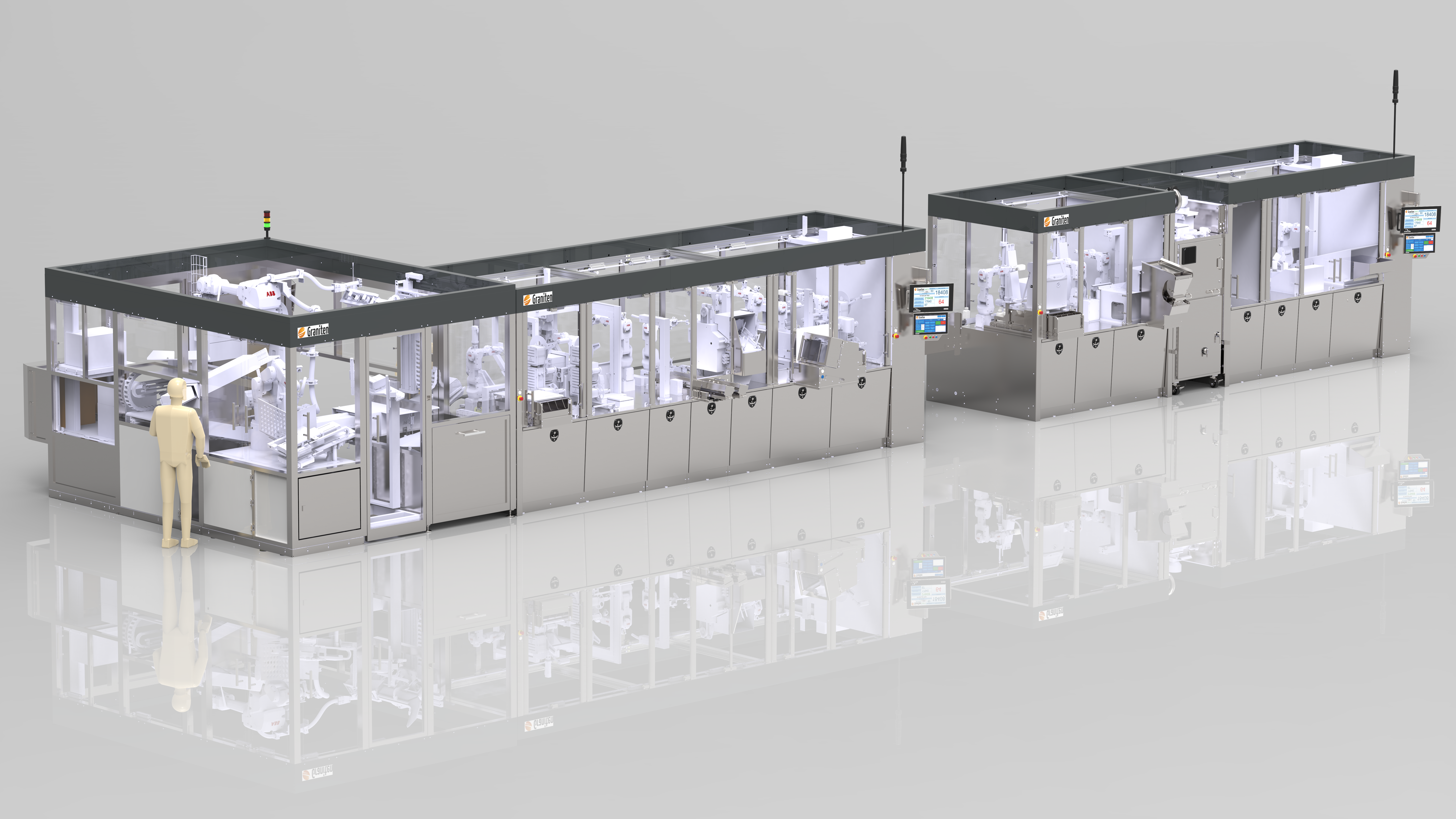
Model showing a full packaging line using the Graniten Flexline solution
Choosing the Right Partner
Selecting the right supplier was a critical step in bringing their vision to life.
After evaluating several options, they chose Graniten and the Graniten Flexline solution, which stood out for its modularity, flexibility, and ability to turn their ideas into reality.
Graniten’s innovative approach offered more than just space savings – it provided a packaging line that could be easily updated and adapted to meet evolving market demands. The modular design allowed for quick replacements and reduced maintenance times, ensuring that production could continue uninterrupted even in the face of challenges.

Key Benefits of the Graniten Flexline
So, what were the key benefits that the customer experienced?
Modularity and Flexibility
The modular design of the Graniten Flexline was a game-changer for the customer as a small-batch manufacturer. Each module could be swapped or upgraded without disrupting the entire line, providing unmatched adaptability. This approach not only simplified maintenance but also allowed the team to keep pace with changing production requirements.
For example, if a particular module required frequent maintenance, a spare could be exchanged to maintain productivity. This flexibility ensured that the line could continue running batch after batch without significant downtime.
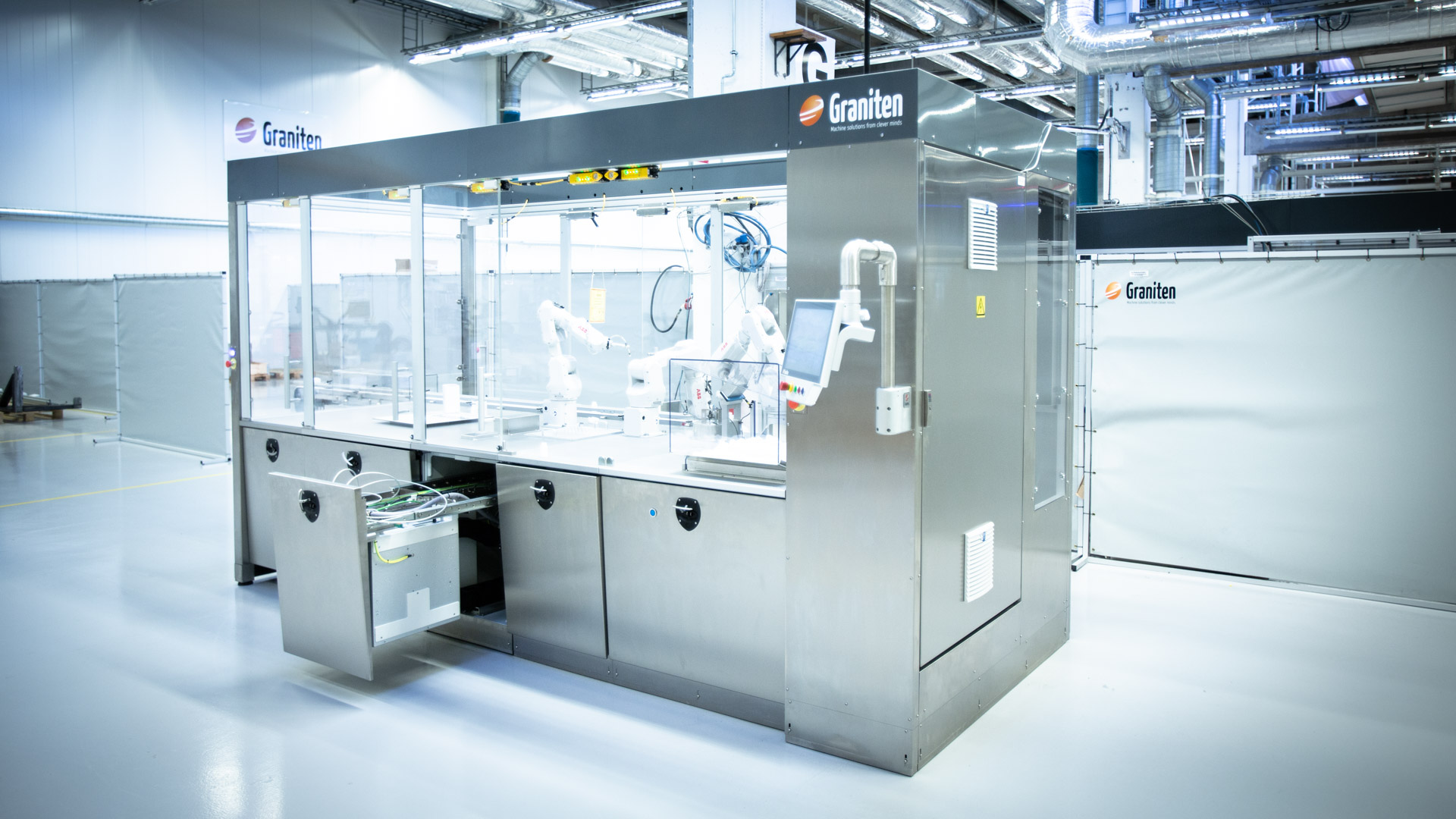
True modularity exemplified
Time savings
The most remarkable outcome was the drastic reduction in changeover time. Previously, changeovers could take up to 8 hours, but with the new system, they were reduced to less than an hour. For instance, switching between shipping box dimensions now involves changing only a gripper to one robot cell – a process that takes mere minutes.
Similarly, handling multiple bottle labels – around 11 different variations – no longer requires manual adjustments to the labelling machines. The streamlined changeover process has freed up valuable time, allowing the team to focus on other aspects of the change over phase (i.e. cleaning, material management, documentation) rather than changing of format parts and set up of the line, obtaining a drastic impact on the overall time between batches.
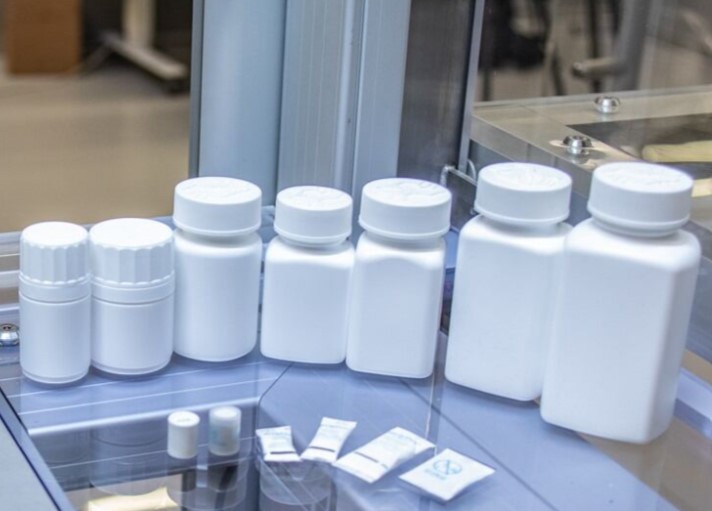
Example of format range
Enhanced Product Security
The Graniten Flexline also brought a new level of product security. Small batches are often handled manually or with semi-automated processes, increasing the risk of human errors. Graniten’s advanced software eliminated this risk by managing all parameters automatically and retrieving them from the overlaying ERP system.
Real-time data exchange between the equipment and monitoring systems ensured that any deviations were instantly identified and addressed. Automated controls for material tracking, fragmentation codes, and quality checks made the process safer and more reliable. This level of automation reduced human intervention, enhancing both security and quality standards.
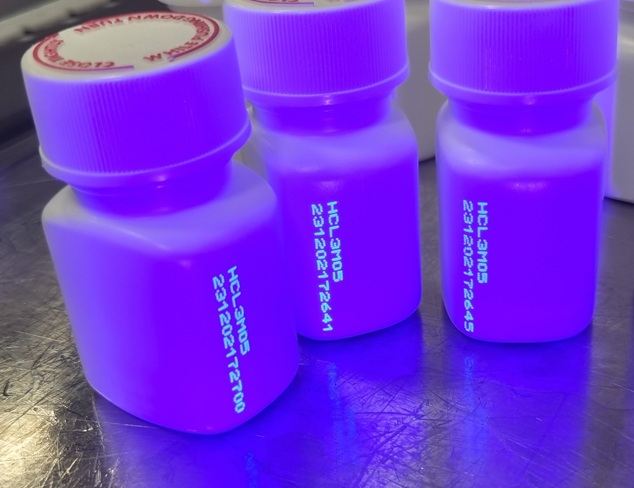
Product tracking UV ink between primary and secondary packaging steps
Lessons Learned and Looking Ahead
What were some of the learnings from the process?
Reflecting on their journey, the customer shared some key insights to other small-batch producers in the pharmaceutical industry:
- Collaboration is Key: Developing a tailored solution required close collaboration between their team and Graniten. This partnership was instrumental in turning their vision into a reality.
- Don’t Settle for Standard Solutions: Traditional methods aren’t always the best fit for unique challenges. Thinking outside the box and exploring innovative technologies can lead to transformative results.
- Invest in Training: Adopting new technology comes with a learning curve. Ensuring that operators and technicians understand the new system is essential for maximizing its potential.
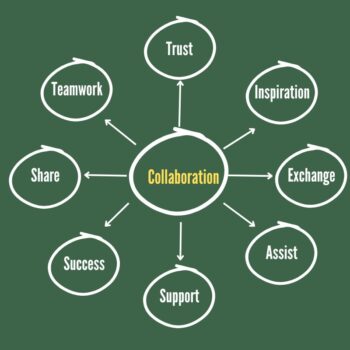
Most importantly this customer’s experience underscores the importance of embracing innovation to overcome challenges.
Their new production line has not only improved efficiency and flexibility but also set a new standard for quality and safety in small-batch pharmaceutical packaging.
Final Thoughts
In summary, by choosing the Graniten Flexline, this customer has redefined what’s possible in small-batch production. The combination of modularity, automation, and advanced software has empowered them to produce life-saving products more efficiently, securely, and sustainably.
Their story is a testament to the power of innovation and collaboration in driving meaningful change – and we’re proud to have played a part in their success!
says Daniel Brännwik, Technology Manager at Graniten.
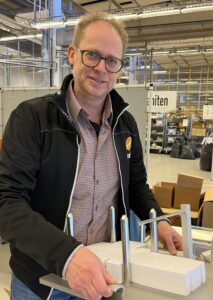
Do you have challenges with changeover time, small batch production or a complex product portfolio, please reach out to us at Graniten.