Complete solution for primary packaging of bottles in small batch pharma production. Makes “payback in days” a fact for manufacturers of high value products.
IN DEPTH
ABOUT
The modular and scalable Graniten Flexline platform, has a close-to-zero (C2Z) changeover time, allowing for an efficient and agile move towards personalized medicine, and ’batch size one’.
This Graniten Flexline example, handles the primary packaging step of filling, and capping plastic bottles, leaving the line as traceable bottles.
The 8 modules selected, correspond to the customer’s specific process needs, but can be altered to fit your process.
- Handling minimum 9 types of bottles (3 round, 6 rectangular), for this example with ø 40-60 mm, and H 60-120 mm.
- Packaging minimum 5 types of caps.
- Scalable & upgradeable – new modules can be easily added or upgraded at a later stage, thereby extending the life of the investment.
- One HMI controlling the entire line, and communicating to the local MES system.
main processes:
- Bottle unscrambling
- Bottle air rinsing
- Desiccant dispensing
- Tablet inspection, counting, and filling
- Manual station (if required)
- Bottle capping
- Cap induction sealing
- Cap retorquing
- Outfeed, reject, and sample point
main features:
- Close to zero changeover time
- Tailormade and modular set-up
- Scalable and upgradable as requirements change
- Minimal footprint
- Low environmental impact
- Good manufacturing practise compliant design
TECHNICAL DATA
Format flexibility:
- Bottle – cuboid (LxWxH): min 40×35×60 mm, max 55×45×120 mm
- Bottle – square (LxWxH): 45×45×80 mm
- Bottle – round (ØxW): min 40×60 mm, max 48×80 mm
- Cap (ØxH): min 35×17,5 mm, max 45×17,5 mm
- Closure (ØxH): min 34×29 mm, max 45×29 mm
- Canister and sachet: A broad range provided
MACHINE DIMENSION RANGE:
- Length 6,75 m
- Width 1,8 m
- Height 2,4 m
CAPACITY:
15 ppm
TECHNICAL CHANGEOVER TIME:
< 3 min. Only the recipe needs to be changed on the HMI, no change parts, allowing minimal order sizes
Curious to find out more?
Complete solution for secondary packaging of bottles in small batch pharma production.
IN DEPTH
ABOUT
The modular and scalable Graniten Flexline platform, has a close-to-zero (C2Z) changeover time, allowing for an efficient and agile move towards personalized medicine, and ’batch size one’.
This Graniten Flexline example, handles the secondary packaging step of filled and closed plastic bottles, leaving the line as traceable cartons.
The 7 modules selected, correspond to the customer’s specific process needs, but can be altered to fit your process.
- Handling 9 types of bottles (3 round, 6 rectangular). For this example with the following dimensions: ø 40-60 mm, and H 60-120 mm.
- Packaging 5 types of cartons from 60x60x100 mm to 85x80x155 mm.
- Scalable & upgradeable – new modules can be easily added or upgraded at a later stage, thereby extending the life of the investment.
- One HMI controlling the entire line and communicating to the local MES system.
main processes:
- Bottle wrap around labelling
- Carton erecting (tuck-in)
- Leaflet folding + bottle insertion
- Booklet feeding + insertion
- Carton closing (tuck-in)
- Vignette + tamper evident labelling
- Carton printing + unit aggregation
main features:
- Close to zero changeover time
- Tailormade and modular set-up
- Scalable and upgradable as requirements change
- Track and trace
- Minimal footprint
- Low environmental impact
- Good manufacturing practise compliant design
TECHNICAL DATA
FORMAT FLEXIBILITY:
- Bottle – cuboid (LxWxH): min 40×35×60 mm, max 55×45×120 mm
- Bottle – square (LxWxH): 45×45×80 mm
- Bottle – round (ØxW): min 40×60 mm, max 48×80 mm
- Cap (ØxH): min 35×17,5 mm, max 45×17,5 mm
- Closure (ØxH): min 34×29 mm, max 45×29 mm
- Canister and sachet: A broad range provided
MACHINE DIMENSION RANGE:
- Length 7 m
- Width 2,1 m
- Height 2,4 m
CAPACITY:
15 ppm
TECHNICAL CHANGEOVER TIME:
< 3 min. Only the recipe needs to be changed on the HMI, no change parts, allowing minimal order sizes.
Curious to find out more?
Secondary packaging line Dosepak® and wallets

Complete solution for secondary packaging of dosepaks® in small batch pharma production.
IN DEPTH
ABOUT
The modular and scalable Graniten Flexline platform, has a close-to-zero (C2Z) changeover time, allowing for an efficient and agile move towards personalized medicine, and ’batch size one’.
This Graniten Flexline example, handles the secondary packaging step where individual blisters are inserted in partitions which are folded and end up in closed wallets or Dosepaks. In turn the wallets/Dosepaks are packaged in outer cartons, which are labelled and identified, ready for tertiary packaging.
The 16 modules or functions selected, correspond to the customer’s specific process needs, but can be altered to fit your process.
- Handling 8 types of blisters, corresponding in 8 types of wallets.
- Packaging 3 types of cartons, and 5 types of booklets and leaflets.
main processes:
- Blister unstacking
- Blank partition unstacking
- Changeover free partition folding
- Blister insertion in partition
- Partition print and verify
- Wallet/Dosepak® opening or folding
- Partition in wallet insertion
- Wallet stacking (multiple wallets can go in a single carton)
- Carton bottom folding
- Leaflet and booklet insertion
- Wallet(s) insertion in carton
- Weighing and carton labelling
- Carton tamper evident labelling
- Carton printing and serialization
main features:
- Close to zero changeover time
- Tailormade and modular set-up
- Scalable and upgradable as requirements change
- Minimal footprint
- Low environmental impact
- Track and trace
- Good manufacturing practise compliant design
TECHNICAL DATA
Curious to find out more?
Primary packaging line blister
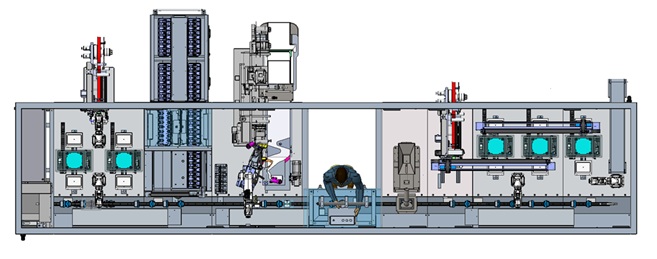
Complete solution for primary packaging of blisters in small batch pharma production.
IN DEPTH
ABOUT
The modular and scalable Graniten Flexline platform, has a close-to-zero (C2Z) changeover time, allowing for an efficient and agile move towards personalized medicine, and ’batch size one’.
This Graniten Flexline example, handles the primary packaging step where blisters are formed from a sheet of material, by using technology from our partner Sepha. Once formed, the blisters are filled with syringes, vials, tablets, etc, and closed by sealing a lidding foil on top. As a last step in the blistering process, the residue is cut away, and a finished blister is ready for further packaging.
The 6 modules or functions selected, showcase some possible functionalities, but can be altered to fit your process.
- Can handle aluminum, PETG, PP, PE, and Tyvek foils
- Can handle blister sizes of up to 140 x 190 mm, with a forming depth of 35 mm.
- Blister printing from Hapa can be added as an additional module.
main processes:
- Foil cutting + blister forming
- Blister feeding with tray-based products such as syringes or auto-injectors.
- Vial labelling and feeding
- Manual feeding station
- Tablet/capsule feeder
- Foil cutter + blister sealing
- Residue cutting and removal
main features:
- Close to zero changeover time
- Tailormade and modular set-up
- Scalable and upgradable as requirements change
- Minimal footprint
- Low environmental impact
- Track and trace
- Good manufacturing practise compliant design